Cement is everywhere. The industry is turning to carbon capture to curb emissions, and it’s not alone
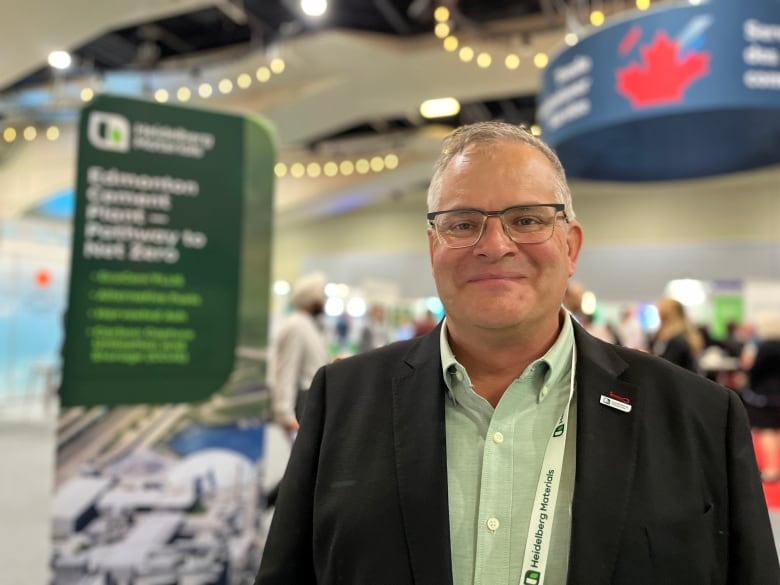
For better or worse, concrete is everywhere. As the second-most consumed material in the world, it’s in the roads you drive on, the foundation of your home and, oftentimes, the walls of the office building that surrounds you.
The problem is, making concrete also pumps carbon dioxide into the atmosphere. Cement, a key ingredient in concrete, is the world’s second-largest industrial CO2 emitter and is responsible for about seven per cent of carbon emissions globally and 1.4 per cent of Canada’s.
But cutting down on those emissions is hard to do. Most of the carbon generated through cement making comes from the fundamental process of heating ground limestone (calcium carbonate), clay and sand at extremely high temperatures in a kiln until it forms small nodules called clinker, which is then ground into cement.
“Since Roman times, this is how it’s been done,” said Corwyn Bruce, a project director with Heidelberg Materials, a German multinational company that makes cement, aggregate and other building materials.
“The carbon is inherent,” said Bruce, who heads up Heidelberg’s Edmonton-based carbon capture and storage project. “It’s literally part of the chemistry.”
Enter carbon capture and storage (CCS).
The technology, which has lately generated lots of buzz within the oilpatch, is also increasingly being seen as a remedy for so-called “hard-to-abate” industries — like cement, iron and steel production — where much of the carbon dioxide emissions are created through process reactions and can’t be eliminated by switching to renewable fuels.
Power plants and fertilizer plants are among other sectors also turning to the technology.
While CCS technology has its limitations — in particular, the geology of where projects are located — the number of CCS projects is on the rise as companies look for ways to decarbonize where no other easy option is available.
Projects underway
At Heidelberg and Lafarge — two of the world’s leading cement manufacturers — work is well underway to marry cement production with carbon capture technology.
Heidelberg has nine carbon capture and storage projects planned across North America, Europe and the U.K. The first two expected to come online are in Edmonton and Brevik, Norway.
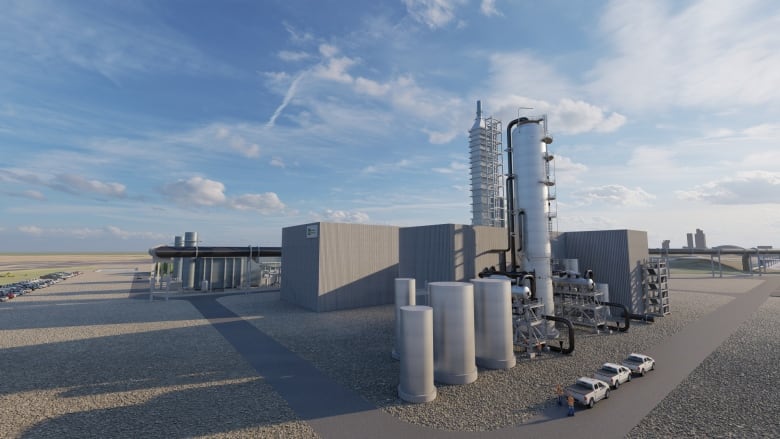
The Brevik plant is expected to capture about 400,000 tonnes of CO2 per year, about 50 per cent of the plant’s emissions, while the company’s Edmonton plant is expected to capture 95 per cent.
That’s largely because of the geology of each location. In Brevik, carbon has to be refrigerated, liquified, put on a boat and sailed around a fjord to be stored under the North Sea.
In Alberta, by contrast, “all we have to do is put it into a pipeline and send it to a storage field,” said Bruce.
Lafarge, for its part, has carbon capture projects underway at both of its cement plants in Western Canada. A detailed feasibility study is underway at its plant in Exshaw, Alta., and it has a carbon capture demonstration project at its plant in Richmond, B.C.
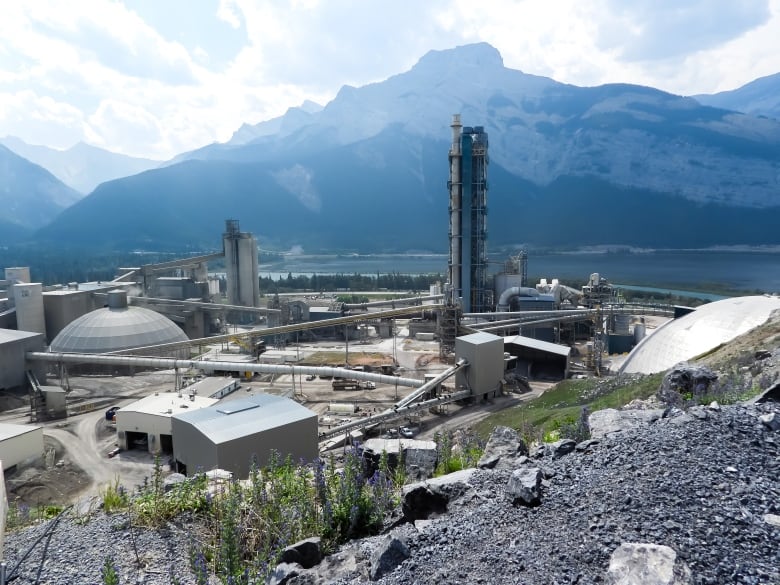
Here again, geology makes a difference.
The Exshaw plant is expected to capture one million tonnes of CO2 per year and sequester it within the Bow Valley, whereas the Richmond plant is planning to reuse its captured carbon for other purposes.
“The sequestration of CO2 in Southern B.C. is less known and more work needs to be done before we can move forward with it,” said Stephanie Voysey, Lafarge’s head of sustainability and environment for Western Canada.
In May, the company announced a new phase of its B.C. demonstration that will see captured carbon used to make synthetic hydrocarbons, which are in turn used for plastics, lubricants and cosmetics.
Outside the cement industry, the Canadian steel sector is also looking at carbon capture as an option to help decarbonize its operations.
That industry, however, is largely concentrated in Ontario, which has only recently opened the door to allowing carbon capture and storage, and there’s still some uncertainty about where that carbon would be stored.
“It’s not just a question for the steel sector, but the larger manufacturing sector … ‘Where is the sequestration?'” said Chad Cathcart, director of research for Hamilton-based Stelco, speaking on a panel at a carbon capture conference in Edmonton this week.
Renewable fuels, reducing clinker
Aside from location, there are other factors that can make or break a carbon capture project.
Even in prime-geology Alberta, CCS projects can be expensive, take a long time to build and can be hindered by factors like labour availability, financing and government policy.
The concrete and cement industry therefore isn’t relying on carbon capture alone to meet its net-zero targets.
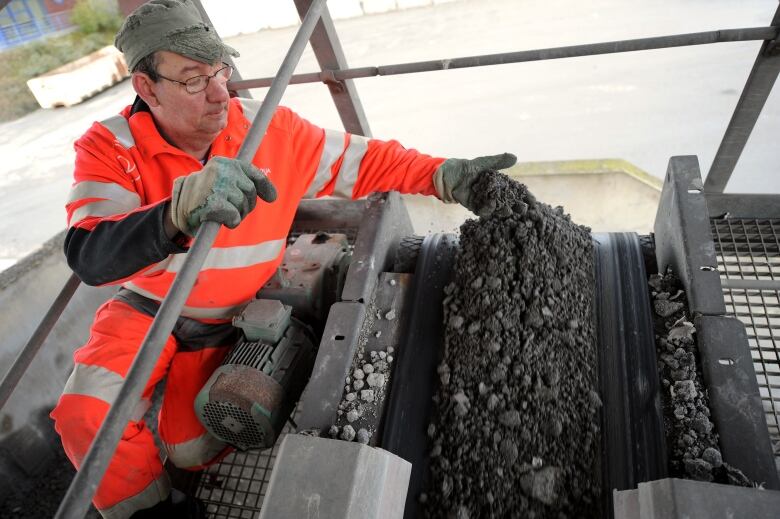
According to the Cement Association of Canada, companies are also eliminating the use of coal and coke as heat sources, ramping up the use of alternative fuels and reducing the use of clinker.
Still, the association noted that despite the limitations, CCS remains the only technology that can eliminate the sector’s process emissions.
“We don’t get to zero without it,” the association wrote in its net-zero action plan.
“Together with bioenergy, clean fuels, and carbon uptake, [carbon capture] could result in the future delivery of carbon-negative concrete for our world.”
Stephanie Voysey, Lafarge’s head of sustainability and environment for Western Canada, agrees.
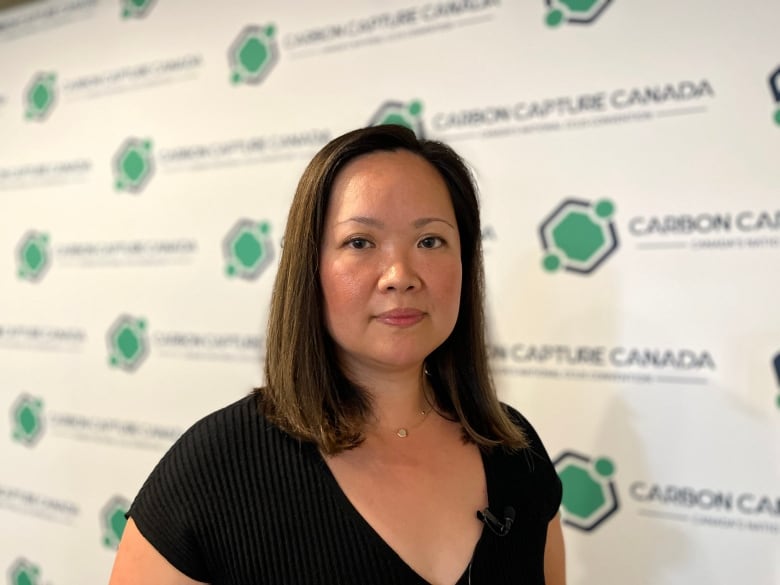
Given how ubiquitous cement is, she noted, it’s crucial to figure out a way to decarbonize it — and the best way to do that, at this point, appears to be CCS.
“We are not going to stop using cement, we’re not going to stop using concrete,” she said. “This is the next step in our innovation in order to reach net zero.”