Guitar maker makes instruments out of mushrooms, beehive
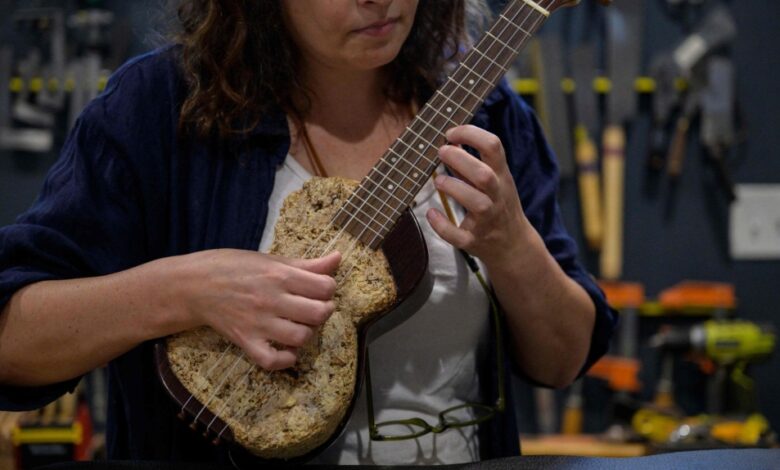
When you think of a guitar what comes to mind? Maybe it’s a simple maple acoustic, the kind played by countless singer-songwriters over the years, or perhaps a double-necked mahogany electric, favoured more by rock-god types.
While these classic guitars will always have a firm spot in our playlists, there are some new designs making waves by harnessing some peculiar materials.
Guitar maker and master luthier Rachel Rosenkrantz thinks she’s hit the right note crafting bespoke instruments out of biomaterials. From mushroom ukuleles and beehive guitars to banjos made out of kombucha leather, she’s assembled a curious collection of biodegradable instruments.
It all began in the early 2000s, when Rosenkrantz was a 21-year-old student in Paris torn between becoming a musician or a visual artist. Guitar-making combined her two passions – but local luthiers said she was too old to start even at that young age – so she stuck with design.
Ten years later and a move to Rhode Island in the US changed her tune. She picked up music again, began her training and has been building guitars for nearly 13 years.
“Maybe it didn’t happen when I was 21, but now I’m 42 and I’m actually doing it, so it’s never too late,” Rosenkrantz told CNN.
Biomaterials entered the picture when she considered the impact guitar-making has on certain tree species.
“Even though we [guitar makers] don’t represent a huge portion of the people that consume wood, we do serious damage in some areas,” Rosenkrantz said. “But I think guitar makers are more conscious about where they get their woods.”
Around 2.6 million guitars are produced annually in the US alone. But unlike the construction and furniture industries, which favour quick-growing timber, the guitar industry typically uses rarer and older woods such as mahogany, ebony and rosewood.
Trees are cut perpendicular to their growth rings for a better sound, and covering an entire guitar’s front, back, and sides means larger logs, like those of old-growths, are needed. Not all of these are sustainable.
Brazilian rosewood was once highly prized for guitars, but the tree, found only in the coastal Brazilian Atlantic Forest, faces serious threats from illegal logging to clear land for agriculture and other uses. Since 1992, its use has been effectively banned by the Convention on International Trade in Endangered Species (CITES).
Sitka spruce has been widely used to make acoustic guitars, but it’s often taken from Alaska’s Tongass National Forest, where widespread logging for various industries has some guitar makers calling for more sustainable alternatives.
“All it takes is to have some ethics,” Rosenkrantz said. “Just doing the right thing makes a big difference.”
THE MUSE
Early in her guitar-making career, Rosenkrantz questioned what could be done without wood and plastics. From her background in design, she saw that biomaterials were being used in everything from BMW cars to sneakers.
Her entry point was replacing plastic with fish skin, which she sources from a vendor in Brazil who makes tilapia leather out of fish farm waste. “It [fish skin] is stronger than plastic, more pliable than plastic,” she said. “For the pick guard that protects the instrument from scratching, it follows the motion of the wood.”
Mycelium – a root-like structure composed of thin threads made by fungi – caught Rosenkrantz’s attention when she saw it used as a packaging replacement for polystyrene. “Polystyrene conducts sound amazingly because it’s full of air,” she observed, “so what if the natural counterpart has the same property?”
Once the material dries, it packs together lots of hollow fibres like a spaghetti bundle, so that it resonates in a similar way to wood, explained Rosenkrantz, who also teaches at the Rhode Island School of Design.
She sources mycelium from a vendor in upstate New York, and says it can be grown in any shape, meaning that working with it doesn’t leave off cuts that go to waste. Her “Mycocaster” electric guitar is made from mycelium and paper, with dried fibres such as corn husk added to make the guitar body more rigid.
THE SOUND
Rosenkrantz’s quirky creations sound slightly different from conventional guitars, depending on the biomaterial they are made from. The “Mycocaster” has a twangy and nasally tone. “I didn’t know it would have that timbre,” she said. However, it did make her think that these instruments could serve niche and perhaps novel genres of music.
“If we want to create new sounds, we might look into new materials,” Rosenkrantz added.
For the Mycocaster, she went a step further by adding some pickups and microphones into the mycelium body which she can adjust depending on how much “mushroom sound” the user wants.
A number of her clients have unusual requests. A musician who composes film soundtracks asked for something that could sound like a range of instruments, so Rosenkrantz made a nine-string baritone electro-acoustic guitar, which incorporated waste fish skin.
Another musician asked for a guitar with two necks, made completely from upcycled elements. The end result is part guitar and part bass, and was made using the client’s 40-year-old pickups, a vintage cigar humidor box as the body, a handle from an old suitcase, and kitchen backsplash tiles as fingerboard markers.
These bespoke guitars don’t come cheap, though. Rosenkrantz’s Mycocaster currently costs US$4,000, and she has three orders in the works. She’d like to bring costs down further, but concedes that she’d need help from a bigger manufacturer.
“I would love for it to be like 50 bucks and every kid can afford one,” Rosenkrantz said. “Maybe a mushroom guitar is a way to actually achieve that, that would be my dream.”
“I have faith in the future,” she added. “What might be considered weird today might not be weird tomorrow.”