UNB researchers using 3D printing to accelerate shipbuilding
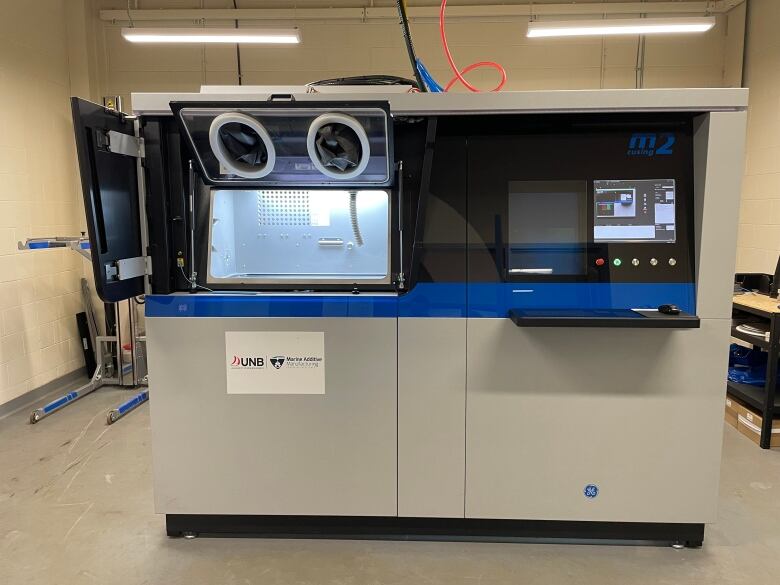
In a Saint John metal fabrication plant, engineers closely monitor a large, humming piece of machinery they believe could transform the speed of ship repairs.
This advanced 3D printer is worth about a million dollars and turns powdered metals into highly efficient parts for the marine industry.
The Marine Additive Manufacturing Centre of Excellence at the University of New Brunswick is one of just a few research facilities in North America looking at 3D printing in shipbuilding.
Mohsen Mohammadi, a professor and director of the centre, said the future ships could have a printer on board to produce new parts while at sea.
“When the ship is protecting our north, protecting our shores, and there is a part that is missing, damaged or failed, the ship does not need to come back to shore. They can easily manufacture one of those as a spare part,” he said.
“That’s how disruptive this technology can be.”
Mohammadi said the technology could also be installed on land in isolated locations, such as the Arctic, to allow for parts to be produced where they typically wouldn’t be available.
The 3D printer starts with digital design files to create specialized ship parts using metal and metal alloys. It then gradually applies incredibly thin layers of metal powder, which are fused together by lasers.
The approach is called additive manufacturing because unlike traditional methods, where metal is removed with a machine to shape it, the material is added layer by layer.
There are several advantages to 3D printing in the shipbuilding industry. The technology allows for the manufacturing of complex parts, it requires limited supplies, it makes it easy to fabricate small quantities and it can cut down on wait times for specialized parts.
The CBC’s Alexandre Silberman explains how a unique 3D printer in Saint John could help ships create spare parts at sea.
Mackenzie Purdy is the 3D print specialist at the research centre and runs the complex machine.
“It’s pretty phenomenal. It’s a unique experience. Even though there’s not very many out there, there’s even fewer in Canada,” he said.
Hamed Asgari, a professor and the centre’s new Lockheed Martin research chair, said the printer can create lighter parts, in turn reducing fuel consumption and greenhouse gasses.
Asgari is currently researching a new concept, known as 4D printing, where the product created has dynamic materials that can change in response to temperature, pressure, humidity and other environmental conditions over time.
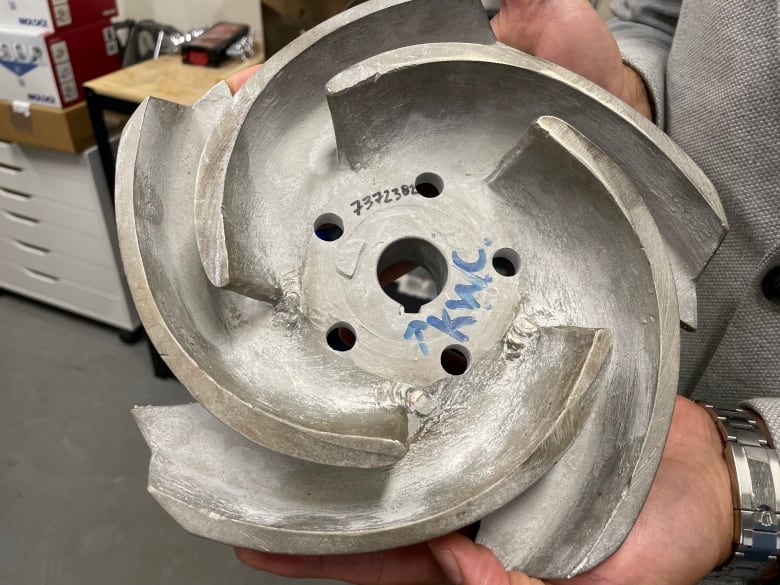
“These alloys are intelligent, they are smart, they are able to change their shape,” he said.
The 4D printing technology could be used to manufacture ship hulls and safety components, allowing the hulls to adjust under different water pressure or temperatures.
The printer at UNB’s facility currently takes several days to print a metal part, even while working around the clock.
Mohammadi said the technology is evolving and is expected to get faster as the printers become more advanced.